螺杆式空气压缩机的演变:2025年终极指南
Author:
Time:2025.03.01
螺杆式空气压缩机极大地改变了工业压缩空气系统,在广泛的应用中提供了卓越的节能性能、可靠的自由空气输送和灵活性。这些压缩机已经发生了显著的变化,从活塞式压缩机的衰落到由变速驱动器和无油技术等创新驱动的旋转螺杆式空气压缩机的兴起。这些技术的发展重新定义了生产率,因此了解喷油和无油螺杆压缩机之间维护要求的差异至关重要。本博客探讨了螺杆压缩机的发展历史,并对这两种技术的维护实践进行了详细的比较。
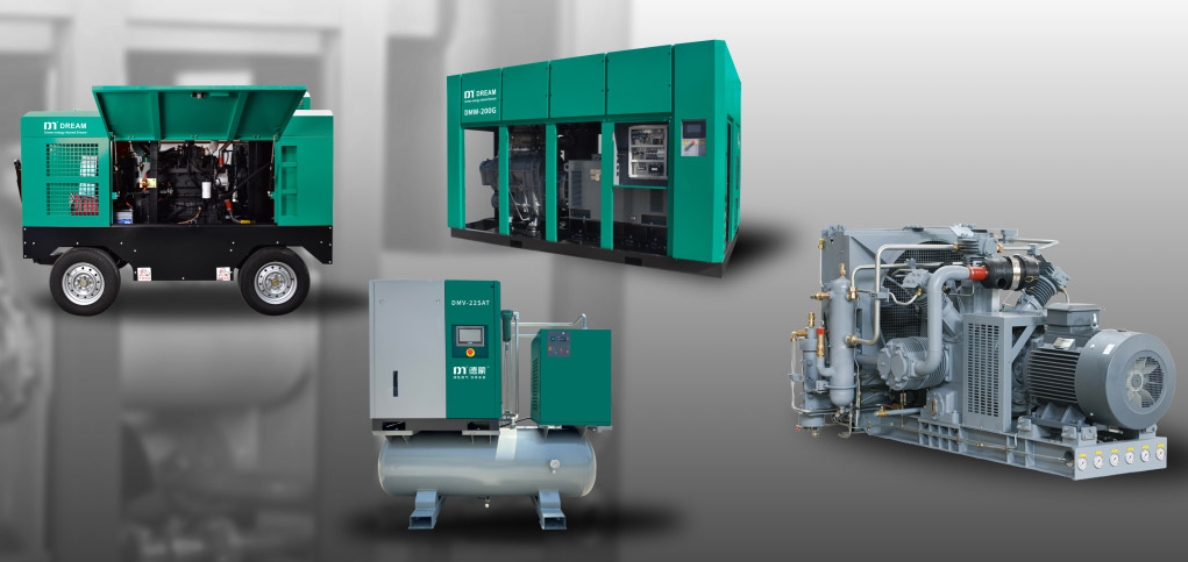
螺杆式空气压缩机的发展历程:从正排量到节能创新
螺杆式空气压缩机的起源可以追溯到20世纪30年代,当时瑞典工程师Alf Lysholm开创了正排量双螺杆设计。最初,这项技术被用于燃气轮机,但直到20世纪60年代,螺杆压缩机才在工业上得到广泛采用。这主要是由于电动机技术和精密制造的进步,与活塞驱动的压缩机相比,这使得压缩机能够实现更稳定的气流和更安静的运行。
关键里程碑:
- 20世纪70年代:喷油螺杆压缩机的引入将油引入系统进行润滑、内部密封和冷却。这显著提高了效率并减少了磨损,使其适用于高占空比。
- 20世纪90年代:无油螺杆压缩机的出现是一个突破,因为它们消除了食品加工和制药等敏感应用中的油携带风险。这是通过先进的涂层和严格的转子公差实现的,确保符合ISO 8573-1 0级标准。
- 2000年代至今:变速驱动器(VSD)和永磁电机的集成优化了节能效果。此外,模块化设计使螺杆压缩机适用于从小型车间到大型制造厂的各种工业应用。
喷油螺杆压缩机与无油螺杆压缩机的维护比较
虽然喷油螺杆式压缩机是一般工业用途的理想选择,但无油螺杆式压缩机在需要清洁、无污染物空气的行业中至关重要。这两种类型都有明显的好处,但它们也有自己的维护需求。让我们分解一下每个的关键维护注意事项:
Core Features:
- These compressors use oil-lubricated systems for sealing, cooling, and noise reduction.
- Suitable for both fixed-speed and variable-speed operations, making them ideal for high-duty cycles.
Maintenance Focus:
- Oil Management:Replace synthetic oil every 4,000–8,000 hours to prevent friction, reduce energy consumption, and prolong compressor life.Change oil filters every 2,000 hours to avoid clogging and overheating, which can compromise efficiency.
- Separator Efficiency:Inspect the oil-air separator every 3,000–6,000 hours. A failing separator can lead to higher oil consumption and contamination of downstream equipment.
- Cooling System:Clean air/oil coolers annually to maintain optimal thermal efficiency and avoid performance loss due to dust buildup.
Advantages:
- Lower upfront costs compared to oil-free models.
- Robust performance in harsh environments.
- Easier repair and maintenance due to widespread serviceability.
Core Features:
- These compressors provide 100% oil-free air, typically using dry screws or water-injected designs, which are critical for industries requiring clean and dry air.
- Often paired with variable speed drives (VSDs) to enhance energy savings.
Maintenance Focus:
- Air Filtration:Clean intake filters every 1,500 hours to prevent particulate damage to rotors.Replace downstream filters (such as activated carbon) annually to maintain air quality and ensure compliance with ISO 8573-1 Class 0 air purity standards.
- Thermal Monitoring:Regularly monitor discharge temperatures (typically <100°C) to prevent overheating, which can damage the rotors or bearings in oil-free systems.
- Bearing and Gear Care:Inspect and regrease bearings and gears every 8,000 hours to avoid dry friction, which can lead to premature wear.
Advantages:
- Zero risk of oil carryover, making them indispensable for applications where even trace amounts of oil can be detrimental.
- Reduced filtration costs since there is no oil to remove from the compressed air.
- Full compliance with strict air purity regulations in industries like food, pharmaceuticals, and electronics.
Future Trends: Smart, Efficient, and Customizable Solutions
As industries push for greater sustainability and efficiency, screw compressors continue to evolve. Here are a few key trends shaping their future:
- IoT Integration: Advanced Internet of Things (IoT) features allow for predictive maintenance, where real-time monitoring of vibration, temperature, and air flow metrics help prevent failures before they occur, minimizing downtime and repair costs.
- Hybrid Designs: Some manufacturers are now combining the best features of oil-free rotors with energy-efficient VSDs to create hybrid screw compressors. These designs focus on reducing the carbon footprint while maintaining optimal performance.
- Customization: Modular designs enable compressors to be tailored to specific needs, whether for low-flow applications or high-pressure systems, offering unparalleled flexibility for industrial users.
Conclusion: Choosing the Right Compressor for Your Needs
When deciding between oil-injected and oil-free screw compressors, the decision depends on the specific needs of your application:
- Oil-injected screw compressors excel in cost-sensitive, high-load environments where the risk of contamination is minimal.
- Oil-free screw compressors are indispensable in industries requiring high-quality, contaminant-free air—making them a top choice for food, pharmaceutical, and electronics sectors.
As technology continues to bridge the efficiency gap between these two options, innovations in quiet operation, energy savings, and smart maintenance will lead the next era of rotary screw air compressors. Whether your priority is upfront cost or long-term air purity, understanding the unique maintenance demands of each system ensures that you select the best compressor for your needs—maximizing performance, longevity, and energy savings.
By leveraging both oil-free and oil-injected technologies, industries can achieve tailored solutions for a broad range of applications, benefiting from reliable, energy-efficient performance in any environment.